Welded Pipe vs Seamless Pipe: Understanding the Differences
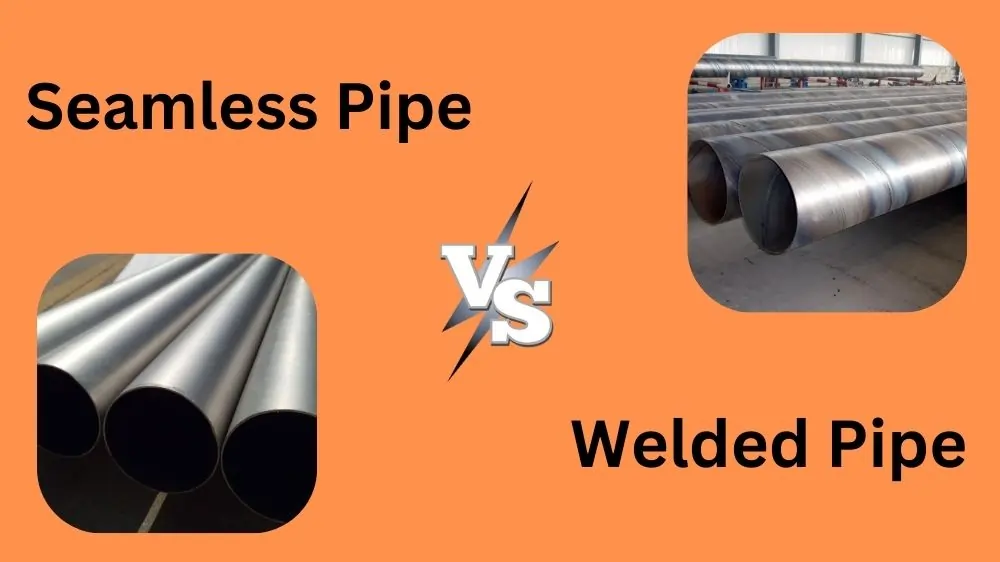
American Steel: Metal Processing Machinery and Industrial Strength
When selecting piping for industrial, commercial, or residential use, the choice often narrows down to welded pipes and seamless pipes. Each type has unique characteristics, advantages, and applications. Understanding these differences is essential for making an informed decision.
Welded Pipe
Welded pipes are manufactured by rolling metal sheets or strips into a cylindrical shape and then welding the seam along its length. They are widely used in applications where cost-effectiveness and availability are priorities.
Key Features
- Manufacturing Process
- Metal sheets are bent and welded to form a pipe.
- The seam is subjected to rigorous testing to ensure durability.
- Sizes and Thickness
- Available in a wide range of diameters and wall thicknesses.
- Commonly used in applications with standard pressure and temperature requirements.
- Cost
- Generally more affordable than seamless pipes due to simpler production techniques.
- Applications
- Water pipelines, structural supports, and low-pressure fluid transport systems.
- Advantages
- Economical and readily available.
- Custom lengths can be produced more easily.
- Disadvantages
- The welded seam can be a point of weakness in high-pressure or high-temperature applications.
Seamless Pipe
Seamless pipes are formed by piercing a solid billet of steel or metal and then elongating it to create a hollow tube. This process eliminates the need for a welded seam, making these pipes more robust for certain uses.
Key Features
- Manufacturing Process
- Produced without seams by extruding metal billets.
- Requires advanced technology and precision.
- Sizes and Thickness
- Typically available in smaller diameters.
- Suitable for high-pressure and high-temperature environments.
- Cost
- More expensive due to complex manufacturing and superior properties.
- Applications
- Oil and gas pipelines, chemical processing, and boiler tubes.
- Advantages
- Higher strength and better performance under pressure.
- No seam ensures uniformity in structure and eliminates weak points.
- Disadvantages
- Higher cost and limited availability in larger sizes.
Comparison Table: Welded vs. Seamless Pipes
Feature | Welded Pipe | Seamless Pipe |
---|---|---|
Manufacturing | Welded from metal sheets | Extruded from solid billets |
Strength | Seam may be a weak point | Uniform strength throughout |
Cost | More economical | More expensive |
Applications | Low-pressure systems | High-pressure systems |
Availability | Wider range of sizes | Limited to smaller diameters |
Customization | Easier to produce custom lengths | Requires specific tooling |
Choosing the Right Pipe for Your Project
- Evaluate Pressure and Temperature Requirements
- Use seamless pipes for high-pressure or high-temperature systems.
- Welded pipes are suitable for standard applications.
- Consider Budget Constraints
- Opt for welded pipes if cost is a significant factor.
- Invest in seamless pipes for critical systems requiring higher reliability.
- Assess Availability
- Check the required sizes and specifications to determine the feasibility of either type.
- Consult Industry Standards
- Ensure the selected pipes meet relevant standards such as ASTM, ASME, or API.
Conclusion
Both welded and seamless pipes have distinct advantages and are suited for specific applications. Welded pipes are ideal for cost-effective, standard use, while seamless pipes are preferred for their superior strength and reliability in demanding environments. By understanding the differences and evaluating project needs, you can choose the right type of pipe for optimal performance and longevity.