Welded Steel Pipes: Comprehensive Guide for Industrial and Commercial Use
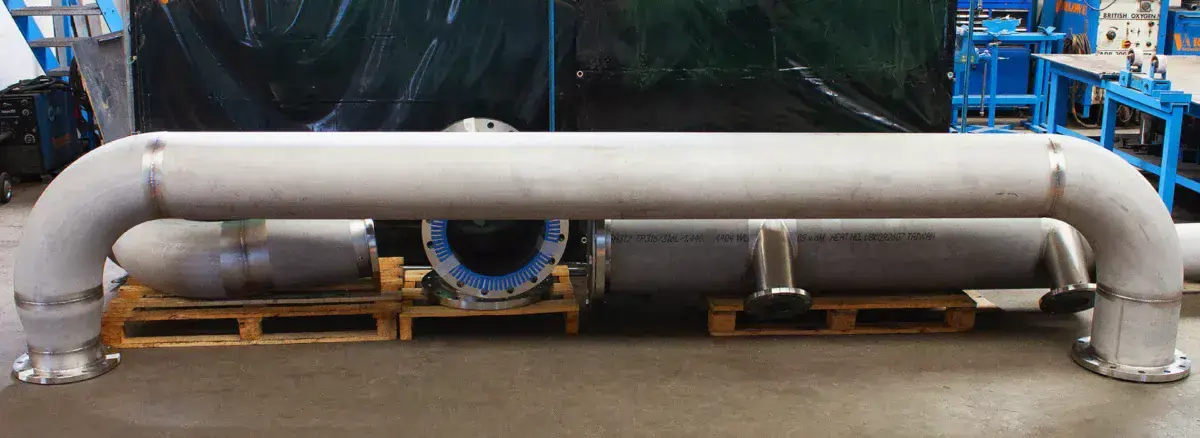
Welded steel pipes are an essential component in modern infrastructure, industrial operations, and construction projects. Known for their strength, durability, and cost-effectiveness, these pipes are widely used in sectors such as oil and gas, water supply, automotive manufacturing, shipbuilding, and civil engineering. This article explores the types, manufacturing process, advantages, and applications of welded steel pipes while incorporating related keywords relevant to global markets.
What Are Welded Steel Pipes?
Welded steel pipes are fabricated by rolling a steel plate or strip into a cylindrical shape and welding the seam longitudinally or spirally. Unlike seamless pipes, which are manufactured through extrusion without any joints, welded pipes are formed by fusing the edges of the rolled material using high-frequency welding or electric resistance welding.
Welded pipes are available in various shapes including round, square, and rectangular profiles. These pipes can be customized according to wall thickness, diameter, and material grade, making them suitable for a wide range of engineering applications.
Types of Welded Steel Pipes
There are several main types of welded steel pipes, classified based on their welding process and application:
1. Electric Resistance Welded (ERW) Pipes
ERW pipes are made from hot-rolled or cold-rolled steel coils and welded using high-frequency electric current. These pipes are commonly used for medium-pressure applications such as water transportation, scaffolding, fencing, and structural purposes.
2. Longitudinal Submerged Arc Welded (LSAW) Pipes
LSAW pipes are produced by bending and welding steel plates in a longitudinal direction. They are known for high strength and are often used in oil and gas pipelines, offshore platforms, and large-scale structural projects.
3. Spiral Submerged Arc Welded (SSAW) Pipes
SSAW pipes are manufactured by spirally bending steel coils and welding the seams. These pipes are typically used in water and wastewater transport, construction piling, and low-pressure industrial pipelines.
Manufacturing Process of Welded Steel Pipes
The production of welded steel pipes involves several stages, including:
-
Steel strip preparation: High-quality steel strips are slit from large steel coils.
-
Forming: The strip is fed into a forming machine that bends it into a cylindrical shape.
-
Welding: The edges of the strip are fused using high-frequency or arc welding techniques.
-
Sizing: The pipe is passed through sizing rollers to ensure uniform diameter and wall thickness.
-
Cutting: Pipes are cut into required lengths.
-
Testing and Inspection: Non-destructive testing (NDT), hydrostatic pressure tests, and visual inspections are performed to ensure product quality.
-
Surface treatment: Pipes may undergo galvanizing, painting, or coating for corrosion resistance.
Advantages of Welded Steel Pipes
Welded pipes offer several advantages over seamless pipes, particularly in cost and availability. Some key benefits include:
-
Cost-effectiveness: Welded pipes are generally more affordable due to the efficient manufacturing process and lower raw material requirements.
-
Availability in large diameters: It’s easier to produce welded pipes in larger diameters and longer lengths.
-
Versatility: Welded steel tubing and pipe products can be produced in different shapes and grades for varied applications.
-
Consistent wall thickness: Modern manufacturing technology ensures precise thickness control throughout the length of the pipe.
Applications of Welded Steel Pipes
Welded steel pipes are used across diverse sectors due to their versatility, including:
-
Oil and gas pipelines: LSAW and SSAW pipes are ideal for transporting crude oil, natural gas, and petroleum products.
-
Water and wastewater: ERW and SSAW pipes are extensively used in municipal water supply and sewage systems.
-
Construction and structural use: Square and rectangular welded steel tubing is widely used in buildings, bridges, stadiums, and airport infrastructure.
-
Automotive industry: Lightweight ERW tubes are employed in the manufacturing of chassis, exhaust systems, and suspension components.
-
Mechanical and general engineering: Welded pipes are used in conveyor belts, steel fabrication, machinery components, and boiler manufacturing.
Related Keywords and Market Demand
As global demand for steel products continues to rise, searches for terms such as “ERW steel pipes supplier,” “welded steel tubing manufacturer,” “SSAW pipe exporter,” and “LSAW pipe factory” are increasingly common. Buyers and procurement agents often seek trusted welded pipe manufacturers in China, India, and Southeast Asia for bulk orders, infrastructure projects, and custom steel pipe production.
Keywords such as mild steel welded pipes, galvanized steel pipe, black welded steel pipe, carbon steel ERW pipe, and heavy-duty welded pipe are frequently used in B2B marketplaces, steel directories, and industrial procurement platforms.
Conclusion
Welded steel pipes serve as a cornerstone for global infrastructure development. Whether for structural support, fluid transportation, or mechanical fabrication, their widespread applicability, combined with economic benefits, makes them a top choice in both industrialized and developing regions. With evolving technology and an increasing focus on quality control and environmental compliance, the welded pipe industry continues to evolve, ensuring its relevance and demand in the decades to come.